We would welcome your help in editing English pages on our site.
Join us.Take part in the Program.
1. Analysis … - 21. Conclusions …
1. Analysis of the facility. Profit. Cost.
Owner of the factory
(Plant) decided to sell it for personal reasons (retirement).
The Plant is in a
working condition with a positive balance, its profitability is about
6% and a net profit is approximately € 280 thousand per year.
The Plant doesn’t have any debts.
The Plant is not mortgaged or under legal
arrest.
The Plant location is quite satisfactory.
The balance value of the Plant is € 11,25
million
The net income of the Plant for 2013 was
approximately € 0,28 million (2.3% of book value).
2. Analysis of the facility.
Construction of a new
Plant with the same capacity can cost 3-4 times higher than its current balance
value.
The plant is suitable
for use as a manufacturing facility for additional products.
Type of the new
products and features of its production must be determined by properties of the
main product – patterned glass.
3. Diagram. Operating mode.
"Black-box” Functional diagram of the Plant
Mode of operation
Plant operating time - 7776 hours
per year (27 days per month).
Time for repair and maintenance -
864 hours per year (3 days per month).
Plant works 24 hours a day in
three shifts.
Management - 8-hour workday.
Number of employees 100.
4. Components. Value. Performance.
Performance.
The maximum capacity of the
furnace - 90 tons per day.
The average theoretical production
- 75 tons per day.
Production losses of glass (fragments)
reused in the production are about 15% (11.25 t).
5. Volume. Price. The main costs.
Average volume of
production (assumed for calculations) is 64
tons/day.
64 tones of glass is
the equivalent of
The market price of
glass - 220-270 €/t
The average price for
calculations - 245 €/t
For reference, in 2013
production reached 60 tons/day at the average
selling price of
The main cost
contributors to production:
Soda ash - 23.05%;
Gas - 30.33%.
6. Structure of production costs.
7. Suppliers. Sales. Waste.
Suppliers of raw materials are
reliable: Bega Minerale Industriale,
Uzinele Sudice-Ciech Chemical Group,
Cominex Nemetalifere, Saint Gobain Construction Products.
Sales of products is determined by
competitive market conditions. Taking into account the development of the
region, sales have a tendency for growth.
Indicators of gaseous waste production conform to
the European standards.
The glass plant does not have
any emissions into water or to soil.
Solid waste is represented by glass
shards, which are reused in the production process.
There is no liquid waste in
production.
Environmental situation is good,
no claims to the plant’s location in the next 20 years are expected.
8. Loss of raw materials during calcinations.
Natural loss of raw
materials occurs due to their thermal decomposition, through exhaust with
carbon dioxide and vaporization with water.
9. Gas conversions.
The combustion of
Production of 64 tons
of glass needs burning of
Incorporation of
breakdown products of soda ash Na2CO3 and CaCO3
chalk oxides into glass Na2O*CaO*6SiO2 also results in
carbon dioxide emission (Na2CO3 → Na2O + CO2;
CaCO3 → CaO + CO2).
To burn
10. Nitrogen release. Conclusion on ecology.
If we consider that the oxygen
represents only 23.15% of the air used
in production, it is clear that along with steam and carbon dioxide the smoke
exhaust will contain
Conclusion about
ecology.
Despite the fact that
ecologists have no claims regarding the purity of combustion gases, it should
be noted that these gases have extremely high content of carbon dioxide. This
undoubtedly contributes to the greenhouse effect. Every ton of glass requires
3.28 tons of air, and overall 4,424 t (3.28 + 0.706 + 0.438) gas mixture (with
the addition of 0,706 t (0,186 + 0,52) CO2 and 0,438 tons (0,013 +
0,425) H2O vapor are emitted into the atmosphere.
11.
A
brief analysis of the market.
The volume of world production of
sheet glass is approximately 54 million tones per year in the amount of nearly
€21.3 billion (about 395 euro/t at the level of production).
Leading companies that
are dominating the market are: Asahi Glass Co. Ltd., Guardian Industries Corp.,
Nippon Sheet Glass Co. Ltd., and Saint-Gobain
S.A. ,
Pilkington
Technician analysts
predict the annual growth of the world market at 9,34% by 2016.
Our Plant produces
about 20 thousand tons of glass per year, or about 0.035% of the world
production.
The price on the glass
at our Plant is below the market value.
There is a tendency for
growth in this market segment.
There is a general
manufacturing opportunity in the glass market.
There is a need to
improve glass production efficiency.
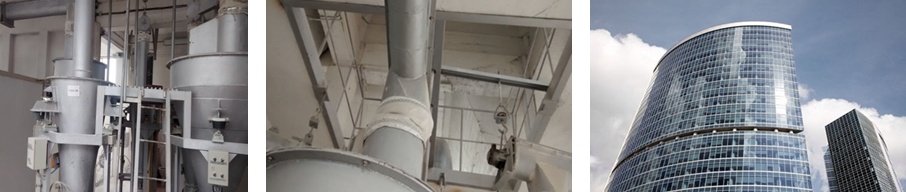
12. World market. Gas emissions.
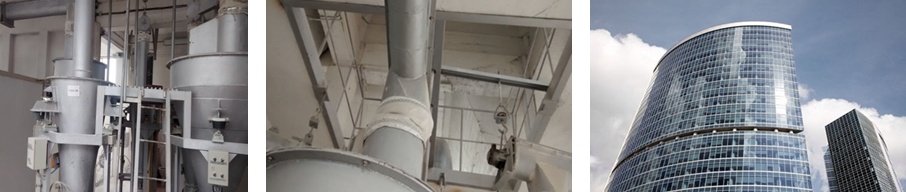
If we apply material
inputs and environmental releases calculated for our plant to global production
of sheet glass (54 million tons/year), it is possible to approximate the volume
of raw materials, carbon dioxide emissions and the nitrogen made by all plants
in the world in one year.
In total, 13 million
tons of soda (amounting approximately €2,8 billion at 215 €/t) is required for
world production of glass; it uses about 10 million tons (14.4 trillion m3) of
natural gas worth around €3,6 billion (250 €/m3 in
Transportation costs
associated with the delivery of soda ash are about 6% of its value - €168
million/year.
13. Conclusions and recommendations.
The most significant
costs for glass production - 53.38%:
- Soda ash Na2CO3, - 0,240 tons at 214,72 € / t
(202.27 + 12.45) - 23.05%;
- Gas,
Following the
principles of compatibility between economic and environmental interests we
formulate the following DIRECTIONS to modernization of the Plant.
We recommend to create
a satellite manufacturing facility dedicated to integration of glass production
into waste-free technological process in 3 steps:
1st step. Implement waste-free
self-production of soda ash.
2nd step. Utilize exhaust gases
with cleaning from sulphur compounds for production of liquefied carbon
dioxide, ammonia, fertilizers.
3-rd step. Replace methane gas
as the main energy source by using organic waste from agricultural and
municipal services, or of industrial origin.
During collection of baseline
data for the design of the 1st step, we can also evaluate the possibility of
parallel implementation of the 2nd and 3rd steps.
New production will be
located at the same premises as the existing glass Plant.
Functional diagram of
the glass production.
The total formula for soda ash
production process corresponds to the theoretical process 2NaCl + CaCO3
= Na2CO3 + CaCl2
Assuming estimated cost of NaCl -
46,00 € / t; CaCO3 - 36,35 € / t; Na2CO3 =
214,72 € / t; CaCl2 - 320 € / t; the costs of production (CP) at
about 50,00 € / t, then the additional revenue from the production of soda ash
for 0.24 t (replacement of purchased), 1 ton and 10 thousand tons, can be
calculated as following:
Substitution of soda
through our own production at the volume of 0.24 t per ton of glass, will
provide an additional revenue of about € 1,9 million per year, which is 5-6
times higher than the income of the current glass production. Total profit will
be about € 2,250 million per year.
The total costs for the
purchase of glass production and implementation of soda production may take
more than 10 years and is not acceptable.
To reduce the period
associated with the project costs, we need to utilize production units of soda ash Na2CO3
– at 10 thousand and calcium chloride CaCl2 – at 10,5 thousand tons
per year.
15. Project’s cost estimate.
The new production
should be about 20 million tons of marketable products per year with income of
about €4,147 million per year (€414,73)/t). This is comparable to the volume of
production of glass in terms of tonnage, but exceeds the profit from the
production of glass (€ 282-373 thousand) by more than 10 times.
Over the period of
licensing the technology for 20 years, the additional Plant revenues will total
€ 82 946 544.58.
Amount of the royalties
in the amount of 5% of the additional revenue will be € 4 147 327.23.
Manufacturing capacity
at 20 thousand tons per year corresponds to a low volume, for which the cost of
the Project is estimated at € 1,5-2 thousand per ton of installed production
capacity.
The base price for
completely new design, construction and equipment installation thus would be €
30-40 million.
Amortization of costs
after 10 years of operation, would result in writing off €3-4 million per year,
which is acceptable considering estimated earnings at €4,147,327 / Year.
Successful launch of
the new production and Project implementation
would allow to correct the basic project costs downwards.
1. For most of the
design, commissioning and construction work we plan to make use of the
south-east European labor force and local population, which would lead to the
base cost at the lower level of € 30 million.
2. Availability of
infrastructure, access roads and communications at the production site, as well
as the existing main buildings and structures reduce the design and construction costs by 1/3, and
allow to drive the base cost of the project further down to the level of € 20
million.
3. Considering that we
plan to use about 50-70% of standard equipment, and subsequent construction at
the site, the project costs can be reduced by additional 1/3 - 1/4 - to € 14
million.
Given the cost of
acquisition of the Plant in the amount of € 9 million the total for the project
costs should be estimated at € 23 million.
This number is
preliminary and tentative, and it will be further refined based on the
development of design documentation and actual expenses.
16. Crediting and earnings.
We need to harmonize
the possible use of credit lines and the potential reduction in base funding
based on the results from implementation of the project.
Reasonable time of
investment - up to 10 years.
The interest rate on
investments or loans - 5%.
We are counting on the
current Plant tax benefit on profits at 16%.
To calculate the
repayment of the project costs we assume:
- Earning from glass
production - at the level of € 0,325 million (€ 282-373 million);
- Earnings from
production of soda - at the level of € 3,94 million (€ 4,147 million minus
royalties);
- Total earnings -
about € 4,2 million (€ 4,265 million).
Full implementation of
our project is expected in 3 years.
3rd year – initiate
pilot operation with an additional income from soda production at € 2,000,000.
/ Year, and total earnings - € 2,3 million.
Subsequent years –
earnings € 4,2 million.
17. Production development plan.
1st year - design
2nd year – equipment construction
and testing
3rd year - trial operation,
unit completion, SOP release.
4th and subsequent
years
- operation.
18. Costs for design and implementation.
We use 3-stage design
(OCD) for the object of 4-5 degree of complexity, excluding stages for
collecting and initial data analysis, - about 30% (€ 4,5 million) costs of the
project. All steps include cost management, design supervision and licensing.
Times required to complete each step may overlap.
19. Return on investment without modernization.
Buying the Plant for €
9 million without modernization (in million €) can be calculated as shown in
the table.
No return on
investments, debt increase.
20. Return on investment with modernization.
Buying the Plant for €
9 million and proceeding with modernization through introduction of new
technology for € 14 million - the full cost of € 23 million, return on
investment is expected in 10 years as shown below.
21. Investment return analysis - conclusions.
1. The glass plant in its current
state and without modernization through introduction of new technologies has no
clear investment value and the prospect of its sale is problematic.
The main reason - the
growing debt on invested capital – up to € 10.57 million in 10 years of service
(if plant is initially bought for € 9 million).
Furthermore, the
investment into existing glass production lines shows no economical prospect.
Co-production and sale
of by-products can be a promising proposition.
2. The volume of glass
production is 20.7 tons per year (64 tons / day * 27 days * 12 months). The
price of the Plant is € 9 million. Based on accepted cost calculations, the
construction of a new plant that would have similar capacity will require
investment of about € 30-40 million. The
return on such large investment is highly questionable. At the same time, the
current plant, at € 9 million, although with a lot of history, is quite
efficient enterprise, and has real prospects of survival and further
development when its profitability is increased.
3. There are two major
avenues to increase the profitability of the plant:
1) reduction of
production costs, production and the use of own raw materials and energy
resources;
2) the production of
by-products.
4. If we develop the
production of soda only for the needs of the plant, the efficiency of
investment will be low. It will be beneficial to introduce the production of
soda ash at capacity of 10 thousand tons and of calcium chloride at 10.5
thousand tons per year. Total production should amount to 20.5 thousand tons
per year.
5.The time needed to
collect initial data towards designing the first phase of modernization can
also be used for analysis and justification of the next steps in Plant
modernization.
Proposed version of
Plant modernization has the following advantages.
1. We can save 20% on
glass manufacturing through our own production of soda ash.
2. We can have
additional production lines that ensure revenues on excess of € 4 million per
year, which is 12 times higher than the currently earned income.
3. There are good
prospects for development of infrastructure and modernization of the company
into the 2nd and 3rd stages.
4. The company can
attract additional advertising through demonstration to the European and the
world community the new satellite glass production - the non-waste production
of soda ash; subsequent disposal of carbon dioxide and the associated
fertilizer production; and the use of new technologies to supply energy.
Join us.Take part in the Program.
We would welcome your help in editing English pages on our site.